Why Should You Use Plasma Spray Solutions?
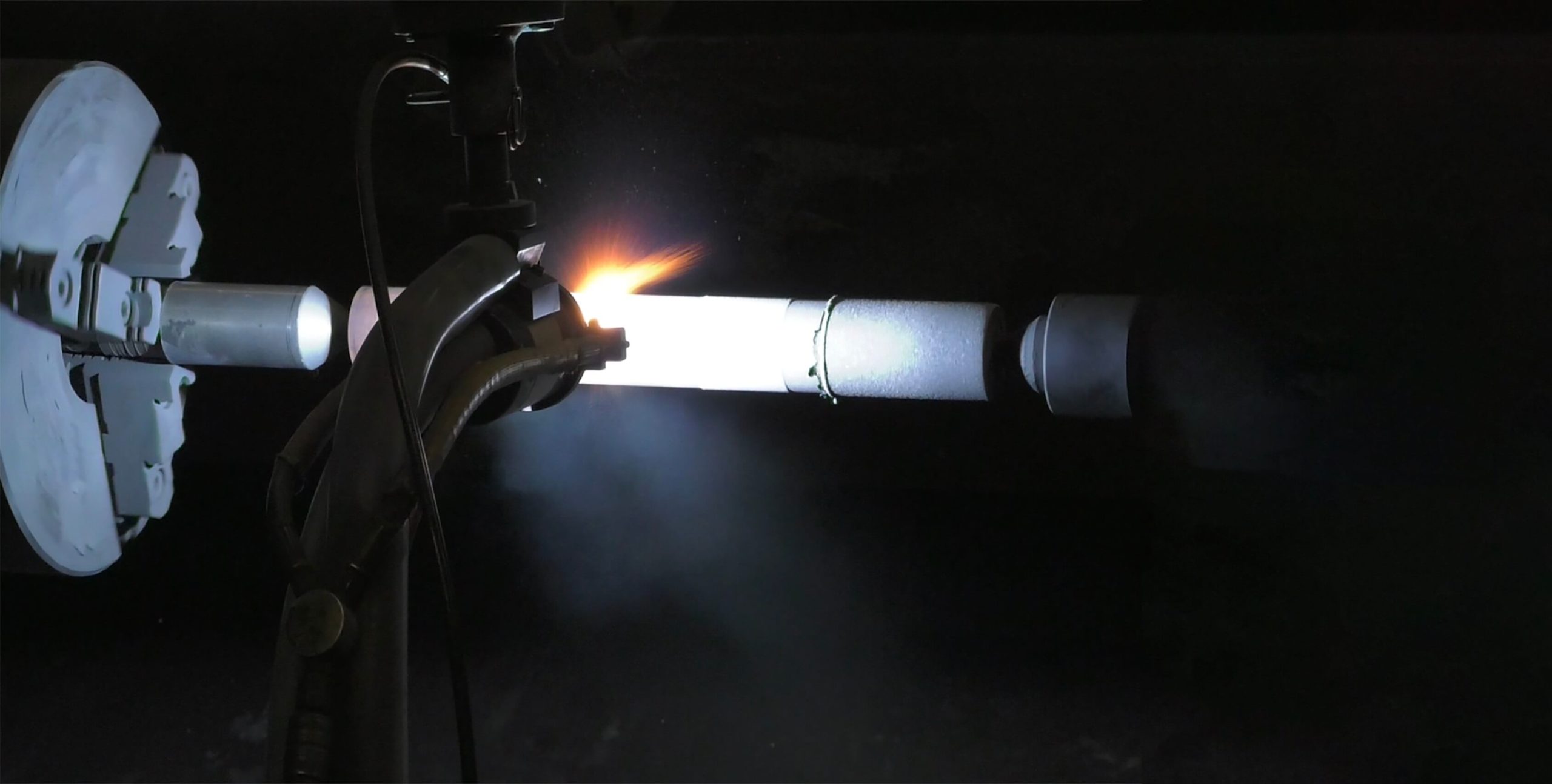
Plasma spray solutions are a highly effective and reliable coating method that can be used to improve the performance, durability, and appearance of a wide variety of industrial components.
But before you decide to use plasma spray solutions for your next project, it’s important to understand what this coating method is and how it can benefit your business. Read along as Wear Master, one of the leading plasma coating companies in Texas, discusses everything you need to know about plasma solutions.
Plasma Spraying: Solutions for Modern Technical Challenges
Plasma spraying is a thermal coating process that uses a plasma torch to heat and melt materials, which are then sprayed onto a substrate surface to form a protective or decorative coating.
This versatile coating method can be used to apply a wide range of materials, including metals, ceramics, and composites. Plasma solutions can also be used to repair and protect components that have been damaged by corrosion, wear, or heat.
This is widely used in the aerospace and automotive industries as well as in medical device manufacturing because of its ability to create smooth, high-quality coatings.
What is Plasma?
Plasma is the fourth state of matter, and it can be found all around us in nature. It’s often referred to as the “fifth element” because it’s so integral to our universe. In fact, 99% of the visible universe is made up of plasma!
On Earth, plasma can be found in lightning bolts, the northern lights, and even in our own blood. When it comes to plasma coating, however, the plasma that’s used is man-made.
Man-made or artificial plasma is created when a gas is heated to such high temperatures that its electrons become detached from its atoms. This process results in a cloud of free-floating electrons and ions that can be used to create a plasma arc. Furthermore, a plasma jet is formed when this plasma arc is constricted by a nozzle.
When this plasma arc comes into contact with a substrate, it vaporizes the coating material and deposits it onto the surface of the substrate in a very thin layer. This process happens extremely quickly, and it can be used to apply coatings that are just a few microns thick.
Fundamentals of Plasma Spraying
Plasma spraying is a type of thermal spraying, a group of processes in which cords, rods, suspensions, solutions, powdered materials, or wires are deposited onto a prepared surface in a molten, semi-molten, or softened state to achieve a uniform coating.
Plasma spray systems differ from other thermal spray systems in that the powder feedstock is heated and accelerated by a plasma heat source in the form of a direct current (DC) arc or radio frequency (RF) discharge. Powder feedstock is injected into the plasma, at which point they are heated and accelerated toward the target surface. On striking the surface, these melted or partially-melted particles flatten and solidify into lamellae or “splats”, gradually coating the surface one particle at a time.
Choosing the Plasma Spray Process
Now that you understand what plasma solutions are and how they work, you might be wondering if this is the right coating method for your next project.
There are a few factors that you’ll need to consider before making your decision, including:
1. The properties of the substrate
When it comes to choosing the best plasma coating process, you must always start by considering the properties of your substrate.
For example, if you’re looking for a coating that can withstand high temperatures, then you’ll need to choose a material that can withstand those temperatures as well. Vacuum plasma spraying is often used to apply coatings to turbine blades and other high-temperature components. Although in general, plasma coatings are best suited for metals, ceramics, and composites.
2. The environment in which the coated component will be used
It’s also important to consider the environment in which the coated component will be used. This is because different environments can have a big impact on the performance of the plasma coating process applied.
For example, if the coated component will be exposed to high temperatures or corrosive materials, then you’ll need to choose a plasma coating that can withstand those conditions. Low-pressure plasma spraying can be used in sensitive environments, such as those that contain food or pharmaceutical products. Atmospheric plasma spraying can be used in more demanding environments, such as those that involve high temperatures or corrosive materials.
3. The desired properties of the coating
Finally, you’ll also need to consider the desired properties of the coating itself. For example, if you’re looking for a coating that can improve the wear resistance of a component, then you’ll need to choose a material that has good wear resistance properties.
Some of the most common properties that are improved by plasma coatings include wear resistance, corrosion resistance, heat resistance, and electrical conductivity.
4. The budget for the project
Of course, you’ll also need to consider your budget for the project. Plasma coatings can be quite expensive, so you’ll need to make sure that you have the funds available to cover the cost of the coating material and the plasma equipment.
If you’re working with a limited budget, then you might want to consider an alternative coating method, such as powder coating or a thermal coating process.
Powder coating is a cheaper alternative to plasma coating, but it doesn’t offer the same level of performance. Thermal spraying is a more expensive option, but it can provide better results.
Key Properties of Plasma Coatings Typical Applications
Now that you know how to choose the best plasma spray coating process for your project, let’s take a closer look at some of the key properties of plasma coatings.
1. Wear Resistance
As we mentioned earlier, one of the biggest advantages of plasma spray coatings is their ability to improve the wear resistance of a component.
This is because the high-velocity particles that are used in the plasma spray process can create a very hard and durable coating. This type of coating is often used on components that are subject to high levels of wear, such as turbine blades, bearings, and pump impellers.
2. Corrosion Resistance
Additionally, plasma spray coatings can offer superior corrosion resistance. This is so that any surface irregularities of the substrate can be covered by a smooth, thick coating produced by the plasma spray process. This kind of coating is frequently applied in environments with corrosive materials, such as chemical industries and oil refineries.
3. Heat Resistance
The capacity of plasma coatings to withstand high temperatures is another important characteristic. This is due to the fact that the high-velocity particles used in the plasma spray process have the ability to produce a very dense and robust covering.
Turbine blades and exhaust systems are two examples of components that frequently have this kind of coating applied to protect against high-temperature exposure.
4. Electrical Conductivity
Additionally, plasma coatings can be utilized to increase a component’s electrical conductivity. This is so that any surface irregularities of the substrate can be covered by a smooth, thick coating produced by the plasma spray process.
Electrical parts like printed circuit boards and electrical connectors frequently have this kind of coating applied to them.
How Does the Plasma Spray Process Work?
Now that we’ve looked at some of the key properties and applications of plasma spray coatings, let’s take a closer look at the plasma spray process itself.
1. The Basics of Plasma Spraying
Plasma spraying is a thermal spray coating process that uses a plasma torch to heat and melt a stream of material. The material is then accelerated to a high velocity and sprayed onto the surface of the substrate.
2. The Plasma Torch
The plasma torch is the heart of the plasma spray process. It consists of an electrode, a gas nozzle, and a power supply. The electrode is responsible for generating the plasma arc that heats the material. The gas nozzle helps to shape and direct the plasma jet. And the power supply provides the electrical energy that is used to create the plasma arc.
3. The Spray Materials
The material that is used in the plasma spray process can be in the form of a powder, liquid, or wire. The powder is the most commonly used form of material, as it is easier to handle and can be melted at lower temperatures.
4. The Spray Process
Once the material has been heated and accelerated to a high velocity, it is sprayed onto the surface of the substrate. The resulting coating will have a very smooth and dense surface.
Plasma Spraying Solutions
Now that we’ve looked at the basics of plasma spraying, let’s take a closer look at some of the different plasma spraying solutions that you might encounter.
1. Thermal Spray Coatings
Thermal spray coatings are the most common type of plasma spray coating. They are typically used to improve the wear resistance, corrosion resistance, or heat resistance of a component.
2. HVOF Coatings
HVOF coatings are a type of plasma spray coating that uses a very high-velocity plasma jet. This kind of coating is often used to improve the wear resistance or corrosion resistance of a component.
3. Plasma Spraying for 3D Printing
Plasma spraying can also be used for 3D printing applications. In this process, a layer of powder is deposited onto a substrate and then melted by a plasma jet. This process is repeated until the desired shape is achieved.
Plasma Coating Companies Texas
If you’re looking for plasma coating companies in Texas, then you should definitely check out Wear Master. We are a leading provider of thermal spray coatings and HVOF coatings. We also offer a wide range of other machine shop services.
So if you’re in need of plasma spraying solutions, then be sure to give us a call today.
Table of Contents
- 1 Plasma Spraying: Solutions for Modern Technical Challenges
- 2 What is Plasma?
- 3 Fundamentals of Plasma Spraying
- 4 Choosing the Plasma Spray Process
- 5 Key Properties of Plasma Coatings Typical Applications
- 6 How Does the Plasma Spray Process Work?
- 7 Plasma Spraying Solutions
- 8 Plasma Coating Companies Texas
- 9 Thermal Spray Coating Services in TX: The Key to Reducing Equipment Downtime
- 10 5 Interesting Facts About HVOF Coating
- 11 CNC Machining Services