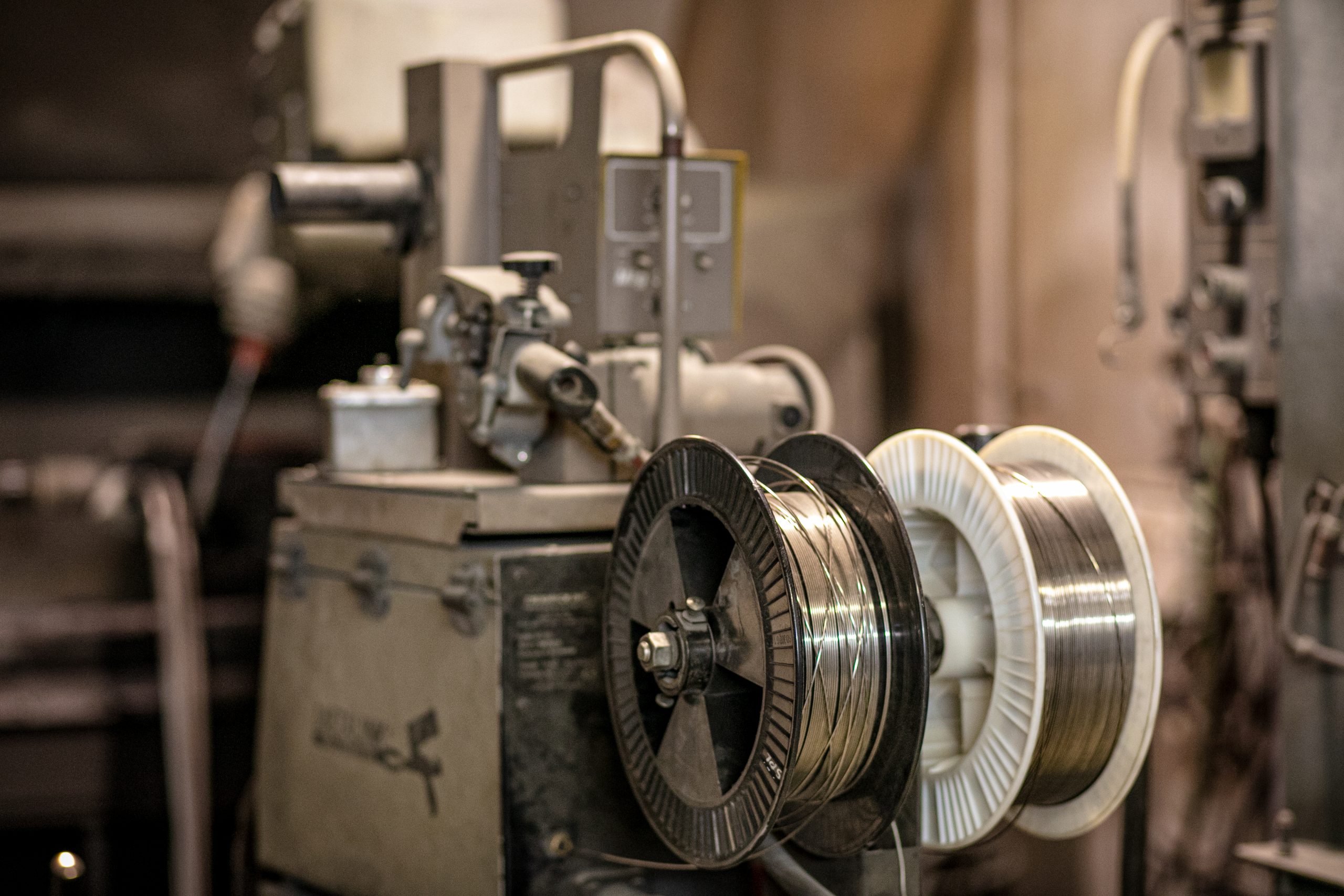
Thermal spray technology provides a cost-effective solution for many applications requiring resistance to wear, heat & corrosion.
With the number of spray technology companies on the rise, it’s important to understand the different types of thermal spray technologies available.
Thermal spraying is a cost-effective way to protect surfaces from corrosion, wear and tear, and extreme temperatures. It can also be used to improve the appearance of surfaces.
Thermal technologies can be classified into different categories, based on the type of spray material used. If you’re considering thermal sprays, it’s important to familiarize yourself with the different types of thermal technology so you can make an informed decision when choosing a provider.
An Introduction to Thermal Spray Technology
Thermal spraying is a coating process in which metallic, ceramic, or polymeric materials are deposited onto a substrate to improve the surface properties of the substrate. Thermal spraying can provide a protective coating of spray materials to a substrate, or it can be used to improve its appearance.
Thermal technology companies use different thermal spray technologies to deposit coatings onto substrates. The most common thermal technologies are:
- Flame spraying
- Electric wire arc spraying
- Plasma spraying
- HVOF (High-Velocity Oxygen Fuel) spraying
Each of these thermal spray technologies uses different equipment and techniques, but they all operate on the same basic principle. We will discuss each thermal technology in more detail in the next section.
Thermal technology companies use a heat source to melt or vaporize the spray material, then they use a high-pressure gas stream to propel the molten or vaporized material onto the substrate.
The result is a coating of the desired spray material that is bonded to the substrate.
Working Principles of Thermal Spray Technology
In all spray processes, the coating material is heated to a high temperature and then sprayed onto the surface of the substrate. The high temperature of the coating material causes it to melt or vaporize.
As the molten or vaporized coating material hits the surface of the substrate, it rapidly cools and solidifies. This rapid cooling causes the coating material to form a bond with the substrate.
Thermal sprayed coatings are typically much thicker than other types of coatings, such as paint or powder coatings. Thermal spray coatings can range in thickness from a few microns to several millimeters.
Furthermore, the type of spray process and thermal barrier coatings used will determine the thermal spray equipment and techniques used to heat and spray the coating material onto the substrate.
Types of Thermal Spray Technologies
Now that you understand the basics of how thermal spray technology works, let’s take a closer look at the different types of thermal spray technologies.

We are a full-service thermal spray shop located in Kennedale, Texas and have been serving the United States since 1983. Let our team be the ones to provide you with the quality thermal spray and machine shop service that you need to make the most of your machinery.
1. Flame Spraying
Flame spraying is the most common type of thermal technology. In this process, the coating material is heated to a high temperature using a flame. The molten or vaporized coating material is then sprayed onto the surface of the substrate using a flame.
Cold spraying is a variation of flame spraying in which the coating material is cooled before it is sprayed onto the substrate.
Flame spraying is typically used to apply coatings made of metals, ceramics, and polymers. The most common types of flame spraying are:
- Metal Flame Spraying: In this type of flame spraying, the coating material is melted using a flame and then sprayed onto the surface of the substrate. Metal flame spraying is typically used to apply coatings made of metals, such as aluminum, brass, and bronze.
- Ceramic Flame Spraying: This kind of flame spraying involves melting the coating material over a flame before spraying it onto the substrate’s surface. Ceramic coatings are comprised of materials like alumina and zirconia.
- Polymer Flame Spraying: Polymer flame spraying is similar to metal flame spraying, except that the coating material is made of a polymer rather than metal. Polymer coatings are typically made of materials like polyethylene and polypropylene.
The advantage of flame spraying is that it can be used to apply coatings made of a wide variety of materials. The disadvantages of flame spraying are that it is not suitable for high-precision applications and that the substrates must be able to withstand high temperatures.
2. Electric Wire Arc Spraying
Another type of thermal technology is electric wire arc spraying. In this process, two electrically charged wires are used to heat the coating material. The heated coating material is then sprayed onto the surface of the substrate using an electric arc.
The process of using this technology involves feeding the coating material through a set of rollers. The rollers compress the coating material into a thin wire. The thin wire is then passed through an electric arc, which heats it to a high temperature. The heated wire is then sent through a nozzle, where it is sprayed onto the surface of the substrate.
Electric wire arc spraying typically produces coatings that are much smoother than those produced by flame spraying. This process is typically used to apply coatings made of metals, such as aluminum, brass, and bronze.
This type of thermal spray technology offers the benefit of being less expensive than other types of thermal technologies. The disadvantage of electric wire arc spraying is that it can be difficult to control the arc and the spray.
3. Plasma Spraying
In plasma spraying, plasma is used to raise the temperature of the coating material to a high level. A gas that has been electrically charged or ionized is what we called plasma.
The coating material is then fed into the plasma jet, where it is melted or vaporized. After that, the molten or vaporized coating material is sprayed onto the surface of the substrate using the plasma jet.
The advantage of plasma sprays is that they can be more precise than other thermal spray technologies. The disadvantage is that it can be expensive and the substrates must be able to withstand high temperatures.
Vacuum plasma spraying, on the other hand, is a variation of plasma spraying in which the process is carried out in a vacuum chamber. One of its main benefits is that it’s more efficient than traditional plasma spraying, meaning that less material is wasted.
4. High-Velocity Oxygen Fuel (HVOF) Spraying
High-velocity oxygen fuel spraying is a type of thermal spray process that uses a high-velocity oxy-fuel flame to heat the coating material. The oxy-fuel flame is created by mixing oxygen and a fuel, such as propane or acetylene.
The high temperature of the oxy-fuel flame causes the coating material to melt or vaporize. The molten or vaporized coating material is then sprayed onto the surface of the substrate using the oxy-fuel flame. This type of thermal technology covers a wide range of materials like metals, ceramics, and polymers.
Some of the main benefits of HVOF are that it produces very smooth and dense coatings. It is also less likely to cause oxidation than other thermal spray technologies. The main downside of HVOF is that it is a relatively expensive process.
Advantages and Applications
There are different advantages and applications for each type of thermal spray technology.
Flame spraying is the most common type of spray process because it is less expensive than other types of spray processes and can be used to apply a wide range of coating properties.
Electric wire arc spraying is typically used to apply thicker coatings than flame spraying. This type of spray process is also less expensive than plasma spraying.
Plasma spraying can be used to apply coatings that are very hard and wear-resistant. This type of thermal spray process is typically used to apply coatings to surfaces that experience high levels of friction or wear, such as engine components.
Coatings with low porosity can be applied with HVOF spraying because they are extremely smooth. The application of coatings on surfaces requiring a high level of precision, such as medical implants, is frequently done using this type of thermal spray method.
Something worth mentioning is cold spraying. Cold spray technology is a newer type of thermal spray process that uses extremely high-pressure gas to atomize the coating material. This type of thermal spray process is less expensive than other types of thermal spray processes and can be used to apply a wide range of materials.
Thermal technology has many advantages and applications in various industries. It is important to choose the right type of spray technology for your particular application.
The Different Types and Applications of Thermal Spray Coating
Thermal coating is the process of applying a coating to a surface by using heat to melt or vaporize the coating material and then spraying the molten or vaporized material onto the surface. Thermal spray coatings can be made of metals, ceramics, polymers, or composites.
The most common type of thermal spray coating is flame spray coating. In this process, the coating material is fed into a flame, where it is melted or vaporized. The molten or vaporized coating material is then sprayed onto the surface of the substrate using the flame.
Other types of thermal coating include electric wire arc spraying, plasma spraying, and high-velocity oxygen fuel spraying. Each type of spray coating has different advantages and applications.
Flame spray coatings are less expensive than other types of thermal spray coatings and can be used to apply a wide range of coatings. Electric wire arc spray coatings are typically used to apply thicker coatings than flame spray coatings.
Plasma spray coatings can be used to apply coatings that are very hard and wear-resistant. High-velocity oxygen fuel spray coatings can be used to apply coatings that are very smooth and have low porosity.
Thermal spray coatings can be used to improve the wear resistance, corrosion resistance, and electrical conductivity of components. Furthermore, this type of technology can also be used to repair damaged components.
Top Four Reasons to Use Arc Thermal Spray
An arc thermal spray is a material coating process that uses heat to melt or vaporize the coating material and then spray the molten or vaporized material onto the surface.
Arc thermal spray has many advantages over other types of thermal processes, including the following:
1. Its application is versatile.
Arc thermal spray can be used to apply metals, ceramics, polymers, and composites. This makes it a versatile coating process that can be used for a variety of applications.
2. It is less expensive than other types of thermal spray processes.
Arc thermal is less expensive than plasma spraying and HVOF spraying because it does not require the use of high-pressure gas. This makes it a good choice for applications where cost is a major consideration.
3. It can be used to apply thicker coatings than other types of thermal spray processes.
Arc thermal can be used to apply coatings that are up to 10 times thicker than those that can be applied with plasma spraying. This makes it a good choice for applications where a thick coating of powder particles from a spray gun is required.
4. It can be used to apply coatings to large surfaces.
Arc thermal can be used to coat surfaces that are up to 100 square feet in size. This makes it a good choice for applications where a large surface area needs to be coated.
Thermal technology has come a long way in recent years, and the arc thermal spray process is a good example of this. This coating process has many advantages over other types of thermal spray processes, making it a good choice for a variety of applications.
Challenges
Despite all the advantages, thermal technology has some challenges. Thermal coatings are typically less smooth and have a higher porosity than other types of coatings. Thermal spray coatings also typically have a shorter lifespan than other types of coatings.
Another challenge with thermal spray technology is that it can be difficult to control the deposition of the coating material. This can result in coatings that are not uniform and have an uneven thickness.
Nonetheless, thermal technology is constantly evolving, and new advances are being made that improve the quality of thermal coatings and overcome some of the challenges associated with this technology.
Table of Contents
- 1 An Introduction to Thermal Spray Technology
- 2 Working Principles of Thermal Spray Technology
- 3 Types of Thermal Spray Technologies
- 4 Advantages and Applications
- 5 The Different Types and Applications of Thermal Spray Coating
- 6 Top Four Reasons to Use Arc Thermal Spray
- 7 Challenges
- 8 Extend the Life of Your Equipment with Wear Master's Thermal Spray Coating Services, TX
- 9 Learn the Basics of CNC Lathe Machining
- 10 Plasma Spray Coating