Plasma Spray Coating
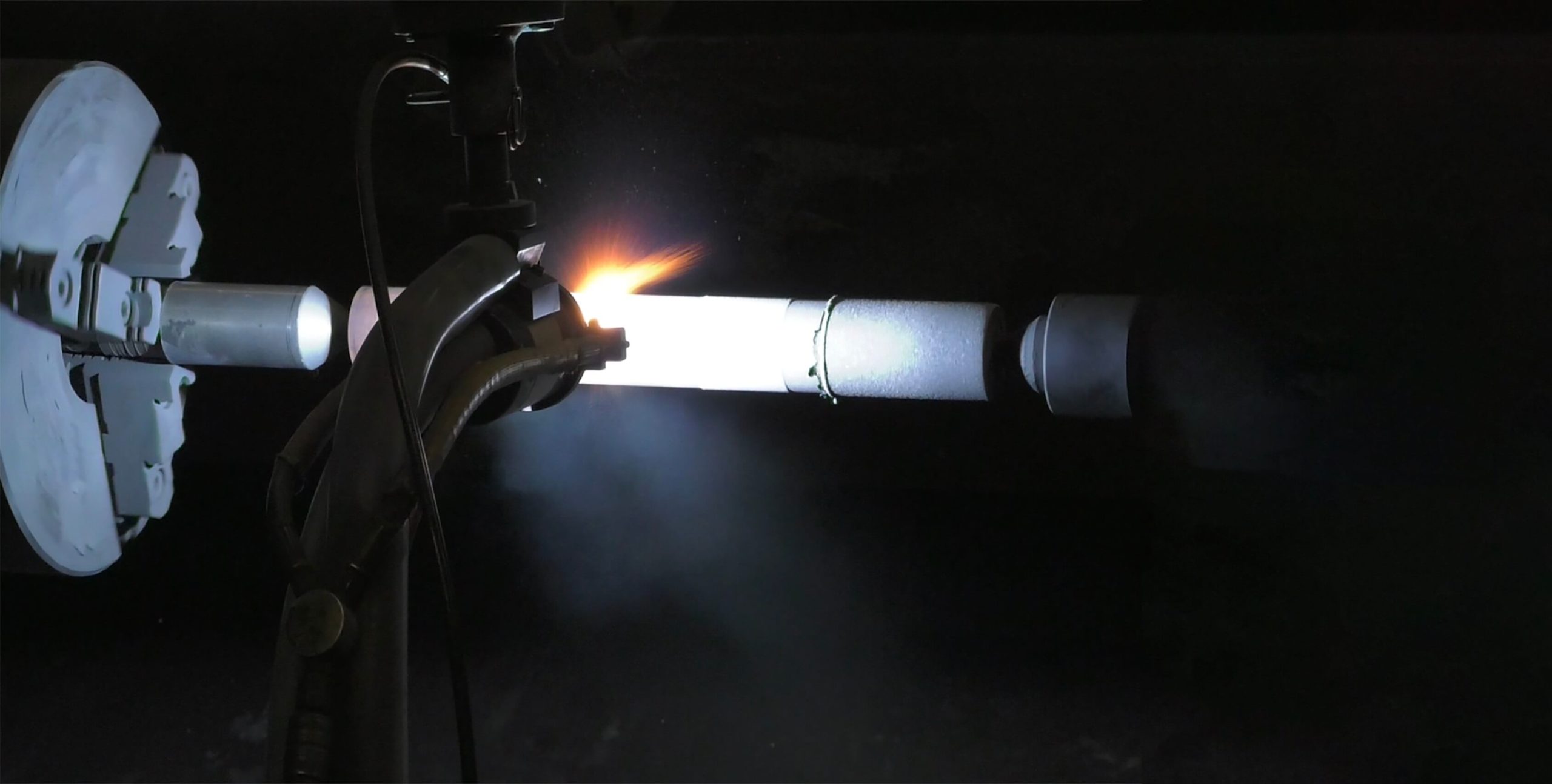
Do you need a protective coating for your metal surfaces? If so, plasma spray coating may be the right choice for you. Here’s everything you need to know.
When it comes to protecting metal surfaces from corrosion, wear and tear, or extreme temperatures, plasma spray coating is one of the most effective methods available. involves spraying a stream of ionized gas (plasma) onto a surface, which then melts and coats the surface with a layer of protective material.
Benefits of Plasma Spray
Plasma spray coating has many benefits that make it an excellent choice for a number of applications. Some of the benefits of plasma spraying include excellent adhesion to a variety of substrates. This helps to create a strong and durable bond that can withstand extreme temperatures and wear.
In addition, vacuum plasma spraying can be applied to complex shapes and geometries, making it ideal for hard-to-reach areas. And because the plasma spray process can be applied quickly and easily, it can help to improve production efficiency and turnaround times.
In addition, plasma spraying is one of the thermal spray processes that can also be used to create a variety of finishes, including glossy, matte, and textured finishes. This makes it an ideal solution for both functional and aesthetic applications.
Common Applications
Plasma spray coating can be used on a variety of materials, including metals, ceramics, and even plastics. It is often used in industries such as aerospace, automotive, and chemical processing where there is a need for high-performance protection.
A plasma spray gun is the main tool used in the plasma spray process. The plasma spray gun produces a jet of hot plasma that melts the coating material and propels it onto the surface to be coated.
Plasma spraying creates wear-resistant, corrosion-resistant, and heat-resistant coatings. This type of coating can also be used to create decorative finishes. This includes creating a variety of colors, textures, and patterns.
Plasma spray coatings are also used in the medical industry for implants and prosthetics. This is because the coatings can create a smooth surface that is biocompatible with the body. The coatings can also be used to improve the strength, durability, and wear resistance of medical devices.
In the automotive industry, plasma spray coating technology is used to protect car parts from corrosion and wear. This includes coatings for exhaust systems, brakes, and engine parts. The plasma sprayed coatings can also be used to improve the appearance of car parts by creating a variety of finishes.
In the aerospace industry, the plasma spraying process is used to protect aircraft components from corrosion and wear. This includes coatings for landing gear, engines, and fuselages. The coatings can also be used to improve the appearance of aircraft components by creating a variety of finishes.
Contact Wear Master
Wear Master is a leading provider of plasma spray coating services. We have years of experience in providing high-quality coatings for a variety of applications. Contact us today to learn more about our plasma spray coating services and how we can help you improve the performance of your components.
Plasma Spray Coating Advantages
Some of the advantages of plasma spray coating include excellent adhesion where it can adhere to a variety of substrates. This helps to create a strong and durable bond that can withstand extreme temperatures and wear.
Compared to HVAF spray, plasma spraying is better suited when it comes to depositing thick coatings. This is because the plasma spray process can deposit a higher amount of material onto the surface. The thicker coatings provide better wear and corrosion resistance.
In addition, plasma spraying produces less heat than other thermal spray processes. This helps to reduce the risk of distortion and warping when coating sensitive materials. And because the plasma spray process can be applied quickly and easily, it helps to improve production efficiency and turnaround times.
Plasma Spray Coating Process Parameters
Aside from the advantages, there are also process parameters you need to consider when using plasma spray coating. These process parameters include the gas type. Argon is the most common gas used in plasma spray coating. Argon is used because it helps to create a more stable plasma jet.
The plasma spray torch power is another important process parameter. The higher the torch power, the greater the deposition rate and particle velocity.
Another crucial process variable is the material’s flow rate during the plasma spray coating process so that the particle size and distribution are not affected. The particle size is also an important process parameter, as it affects the microstructure of the coating.
Finally, the substrate temperature is also an important process parameter. The substrate temperature affects the deposition rate, microstructure, and properties of the coating.
FAQ
WHAT IS PLASMA SPRAY COATING?
Plasma spray coating is a process that uses plasma to deposit a coating onto a substrate. The plasma is created by ionizing a gas using an electric arc. The resulting plasma jet is used to melt and propel particles of coating material onto the substrate.
WHY ARE COATINGS HEATED BEFORE SPRAYING?
It is important to heat the coating material before spraying because it helps to improve the adhesion of the coating. In addition, heating the coating material helps to reduce the risk of defects and improve the overall quality of the coating.
DO THE COATINGS REQUIRE FINISH MACHINING OR GRINDING?
No, the coatings do not require finish machining or grinding. The plasma spray process can be used to create a variety of finishes, including glossy, matte, and textured finishes. This means that the coatings can be used for both functional and aesthetic applications without finish machining or grinding.
IS A DRYING OR CURING PERIOD REQUIRED AFTER THE COATING IS APPLIED?
No, a drying or curing period is not required after the coating is applied. The plasma spray process creates a cross-linked structure that is immediately ready for use. This means that there is no waiting period required after the coating is applied.
WHAT IS THERMAL SPRAY COATING?
Thermal spray coating is a process that uses heat to melt and propel particles of coating material onto a substrate. The resulting coating has excellent wear and corrosion resistance properties.
The main difference between plasma spray coating and thermal spray coating is the way in which the coating is applied. Plasma spray coating uses plasma to melt and propel the coating material, while thermal spray coating uses heat. This means that plasma spray coatings have a higher deposition rate and are more efficient than thermal spray coatings.